What do you get when you feed bacteria with industrial fruit waste? “A yellow leather jacket” might not be your first answer, but it’s exactly what came out of a collaboration between Danish fashion brand Ganni and Mexican biomaterials company Polybion.
The blazer — a one-of-a-kind prototype that is meant as a proof of concept for future collections — is made from bacterial cellulose, and rather than trying to replicate the characteristics of leather, it’s designed to feel like an entirely new material.
“We were impressed by the fact that a lot of people love the jacket because the material did not resemble leather,” said Alexis Gómez-Ortigoza, Polybion’s co-founder. “It’s really easy to recognize that this is not leather — but also that it’s not plastic. It has a unique feel to it.”
Although it is produced using some of the methods associated with traditional leather, the blazer has a much smaller carbon footprint, without compromising on strength and breathability, say its creators. “This is the first jacket ever made by a global brand out of bacterial nanocellulose,” added Gómez-Ortigoza, “So it is a pretty important milestone for the biomaterials industry.”
From kombucha to canned fruit
Gómez-Ortigoza, whose background is in finance, founded Polybion in 2014 with his brother, Axel, whose background is in biotechnology. Together with friend and materials scientist Bárbara González Rolón, they initially focused on mycelium, a root-like network of fungal threads, and opened a pilot plant for mycelium materials.
Then, something peculiar happened. “About five years ago, a friend of mine stepped into my office and he showed me a kombucha jar,” recalled Gómez-Ortigoza. “We isolated our first bacteria from that drink.”
Kombucha is an increasingly popular fermented tea drink, and the bacterial biomass used to make the jacket, called Celium, comes from that jar. Since then, Polybion has almost entirely pivoted to bacterial fermentation, as it deemed it a promising new source for a high-performance leather alternative.
To feed the bacteria, Polybion uses scraps sourced from local canned fruit production plants, mainly from mangoes. “We feed the bacteria with fruit waste, which is extremely abundant here in central Mexico,” said Gómez-Ortigoza. “We turn it into food for the bacteria by adding a special formula developed by us that converts it into a growth medium.
“The bacteria will then reproduce and generate the nanocellulose matrix as a metabolic byproduct, which we harvest after two weeks and then send through a tanning and finishing procedure.”
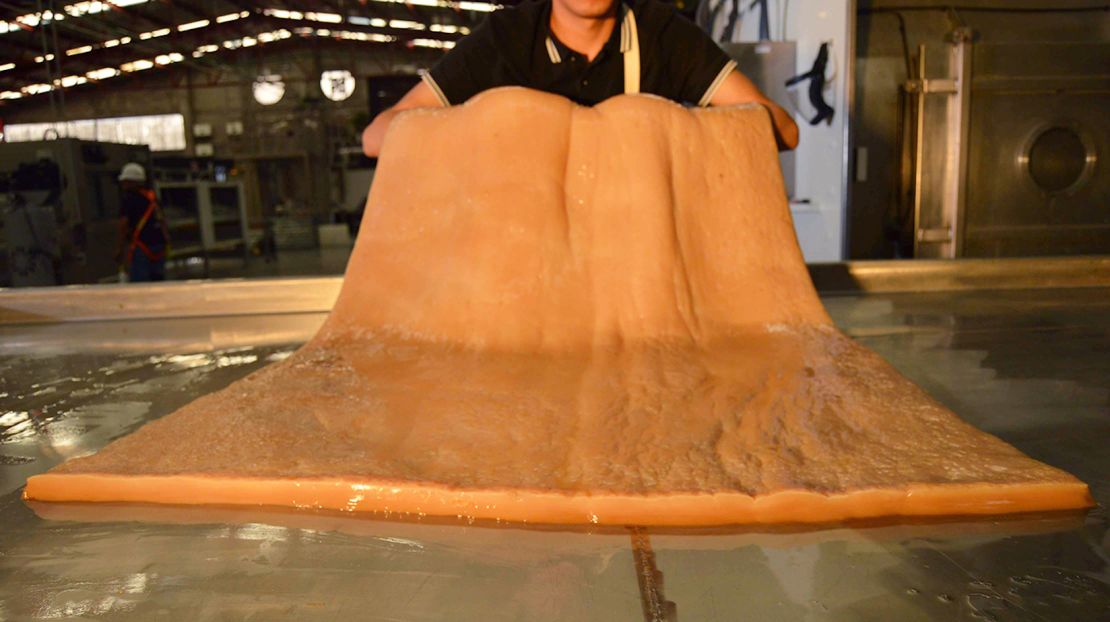
The fruit waste would otherwise end up in a landfill, where it would decompose and generate methane — a greenhouse gas 25 times more powerful than carbon dioxide at trapping heat. Some producers, according to Gómez-Ortigoza, also burn or dump the waste illegally. The production of Celium creates about one quarter of the emissions compared to the greenest methods of leather production, and after factoring in the emissions avoided by rescuing the fruit waste, the process becomes carbon negative, Gómez-Ortigoza said.
Once the nanocellulose is harvested, it is treated using techniques employed by local tanneries. “We use the same equipment as animal leather tanneries, but without chromium or any toxic chemicals,” said Gómez-Ortigoza. “Since this material is organic, it has a natural feel to it — it breathes and wears out in a similar way to leather. This is really important, especially for luxury brands.”
Polybion is exploring the possibility of using Celium to make something other than textiles, including cardboard, thread, construction wood, and even wound dressings. “It has the potential to become a commodity, a widespread material for a different range of applications,” Gómez-Ortigoza added. “But as of right now, we are focused on a leather alternative, because we believe this application has the shortest time to market.”
Cut from a different cloth
If you want to buy a bacterial jacket, you’ll have to wait just a little bit longer. “The blazer is a one-of-a-kind piece and unfortunately not for sale,” said Lauren Bartley, Ganni’s Sustainability and CSR Director. Ganni, which has committed to a 50% absolute carbon reduction for its operations by 2027, is working with other new types of fabric, with the aim of making 10% of its main collection from them by 2025. However, the company will be selling garments made from Celium in 2024.
The design of the blazer is the same silhouette that Ganni successfully featured in previous collections using traditional materials — worn by Michelle Obama in an organic cotton version, Bartley says. “We went for a yellow color to give it the same bright feeling and impact as the versions of the blazer in bright pink and green made in wool in previous collections,” she adds.

Polybion is planning similar projects with other fashion brands, although it won’t reveal the names yet. “All I can say that we are working with the biggest sportswear company in the world as well as three of the most important luxury fashion houses from France,” said Gómez-Ortigoza, adding that he expects to announce these in detail next year.
Fashion houses are increasingly exploring innovative materials as a way to make their garments more sustainable. “The textile industry is looking to agricultural and food waste as a viable raw material for this new material revolution in response to the climate crisis, making better use of planetary resources without the need to use virgin ones,” said Kate Goldsworthy, a professor of Circular Design and Innovation at the University of the Arts London, who’s not involved with Polybion.
“Textiles made from cellulose are certainly not new, but a growing range of innovative companies are finding new ways to produce cellulose fibers from waste streams. Polybion have considered the environment in every aspect of their production, and the supply chain is contained within a 30-mile radius, taking local production seriously,” she said, adding that the challenge is now scaling up production and getting consumers to embrace the materials as well.
According to Kate Fletcher, a professor at the Royal Danish Academy, Copenhagen and Oslo Metropolitan University in Norway, while alternative materials like Celium are a welcome addition to the range of fabrics promising lower-impact clothing, this will never address the root cause of the sustainability challenge for fashion.
“This challenge lies elsewhere: in addressing the year-on-year growth in scale of the fashion sector and reducing overproduction, without which impacts will continue to rise regardless of what material we make garments in,” she said.